In a strategic move to enhance our rapid prototyping and manufacturing capabilities, we have incorporated two Bambu Labs X1E printers into our additive manufacturing fleet. These printers represent high-speed, high-quality additive technology, offering versatility and precision in rapid prototyping.
The Bambu Labs X1E printers are distinguished by their speed, enabling rapid production cycles that significantly reduce the time from concept to prototype. This rapid printing capability is beneficial for projects where time efficiency and the ability to iterate designs quickly are important.
Each unit is engineered to produce high-quality prints with fine detail and smooth finishes, useful for the intricate components and prototypes common in aerospace applications. The precision of the Bambu Labs X1E ensures that even complex designs can be accurately reproduced.
Capable of working with a wide range of materials, these printers allow us to explore new design possibilities and materials engineering, from standard thermoplastics to advanced composites. This versatility supports our commitment to innovation and enables us to tailor solutions to the specific needs of our projects and clients.
If you’ve read the article about our five-axis CNC machine, you’ll know that we used our Bambu X1Es to print stiffening brackets to improve the accuracy and repeatability of our machining capability. These brackets were designed by our AM manager Garry Sellick with additive manufacturability in mind using DfAM (Design for Additive Manufacturing). We used Carbon Fiber Reinforced Polylactic Acid (CF-PLA) for this unique project due to its enhanced stiffness and strength, dimensional stability, durability, and ease of printing.
As we continue to leverage the capabilities of the Bambu Labs X1E printers, Airframe Designs is well positioned to meet the evolving needs of our clients with efficiency and precision.
Recent projects undertaken by Airframe Designs include the design and manufacture of several 3D printed tooling fixtures to aid the installation of external sensors onto the fuselage of a special mission military aircraft and the integration of new systems into heavy lift drone platforms.
The company has also been responsible for the conceptual design at a platform level for new uncrewed air-systems, test rig and tooling for electric vehicle propulsion systems and most recently the design and analysis of operator consoles for a special mission aircraft.
For more information contact Airframe Designs, tel 01253 400320 or fill in a contact us form here.
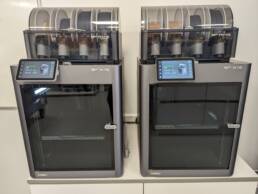
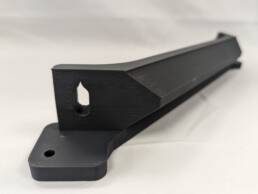
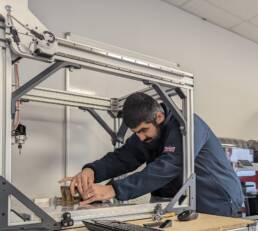