Capabilities
Our core capabilities cover traditional static stress analysis (hand calculation), FEM (Finite Element Modelling), and F&DT (Fatigue and Damage Tolerance) evaluation.
We also provide support in the assessment of vibration, bird strike, and aerodynamics, including computational fluid dynamics.
For traditional static stress analysis, we use a combination of hand-calculations, MATHCAD computation, Excel Spreadsheets, and PYTHON scripting to check the strength of metallic, non-metallic, and composite structures.
We perform analysis to suit the client needs whether this be initial sizing to support conceptual design phases, or final design calculations to support project certification submissions.
Our primary finite element modelling tool is MSC ONE with PATRAN and APEX pre and post-processors and NASTRAN code. This provides an advanced meshing and generative design capability that streamlines CAD clean-up and simplifies the meshing and modelling workflow.
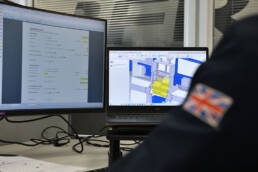
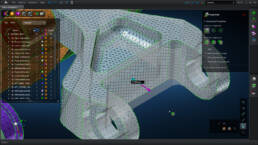
Our engineers are highly familiar with the techniques employed for modelling airframe thin-walled structures using beam and shell elements (e.g. major fittings) using 3D TET or HEX solid elements.
We perform Fatigue Analyses using either a stress-based (s-N) or strain-based (e-N) approach and develop the necessary analysis tools from first principles to suit the analysis requirements and needs of the customer.
For Damage Tolerance we conduct a crack growth assessment using in house scripts, client-supplied software, or commercially available tools such as AFGROW or NASGRO.
We have extensive knowledge in the F&DT assessment of fuselage penetrations for antenna feed throughs and the substantiation of modified Fatigue Critical Structure.
Lisa ChambersStructures Manager
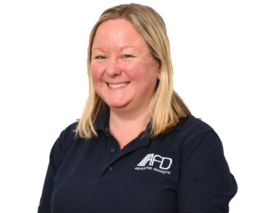
A very experienced principal stress engineer with an aptitude for leadership and team management.
Lisa began her career at British Aerospace (now BAE Systems) as an Apprentice Fitter before progressing into the Stress Office at Warton, Lancashire.
After 8 years at BAE Systems, Lisa spent some time as a Senior Lecturer in Engineering at Blackpool & the Fylde College before returning to industry.
Lisa has worked for Bombardier in Canada, Jet Aviation in Switzerland, and SAAB in Sweden, but decided to return home to Blackpool in 2019 and join Airframe Designs in a leadership role.
She has over 20 years’ of experience in the Aviation Sector and is appointed as a Structural Compliance Verification Engineer (CVE) for several UK and European customers.
As the Structures Manager, Lisa leads the entire team of Stress Engineers to ensure that benchmark processes are being followed and on-time delivery is accomplished, to the right quality, and within budget.